From continuous improvement to constant innovation: a reflection.
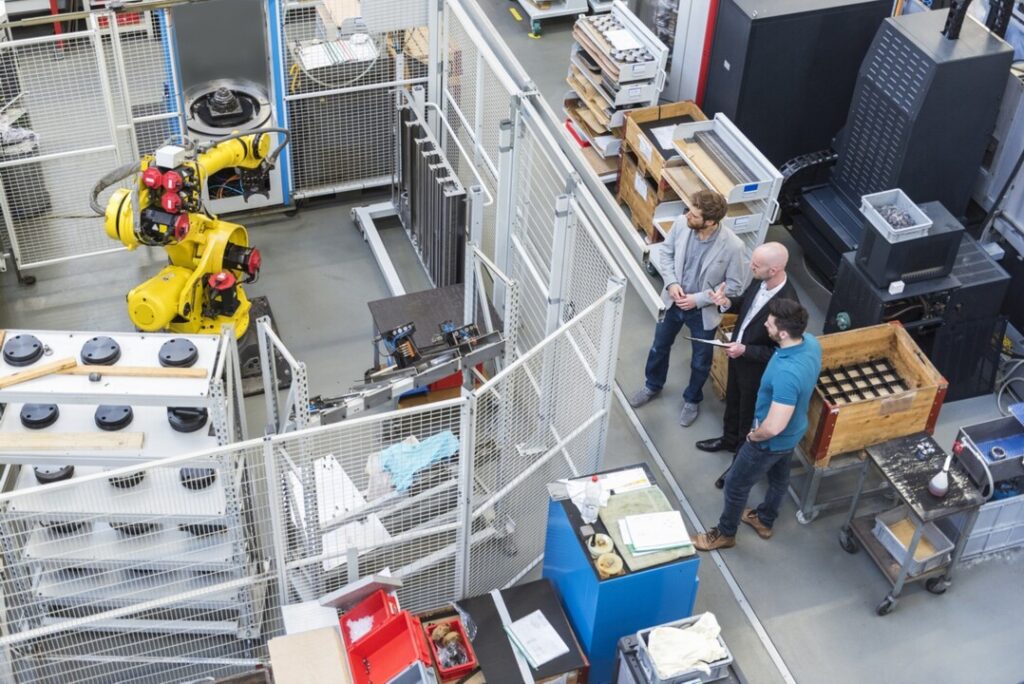
In today’s hyper-competitive business environment, organizations are innovating around the clock. Teams facilitating the same at firms, are transforming fundamentally to unlock great value. At this juncture, “continuous improvement” becomes an effective transformation strategy. In a way, it is the main name in the industrial game. Research has proved that successful continuous improvement efforts can lead to significant process enhancements. Several manufacturing giants and Fortune 500 companies have exemplified the same, time and again.
I started my career about 28 years ago from today. During my stints at Toyota and GE respectively, I observed how the manufacturing firms were implementing KAIZEN™ to continually yield superior results. As I recollected my experiences at these companies, I realized that to successfully build a culture for continuous improvement, people in an organization must engage fully and become a part of the process.
To begin with in today’s scenario, a team can change its mindset, by embracing “continuous innovation.” That means, they may combine operational effectiveness and strategic flexibility — to explore the capabilities, that have traditionally been regarded as antithetical. In other words, there is room to improve and reflect in every operational process.
Incremental changes can lead to exponential results
It is impossible to radically restructure your organization in a single day! So, focus on each business process from the ground up.
Here’s how you can start:
1. Create an exponential mindset for yourself (and your team). You should be comfortable with uncertainty. That way, every single incremental effort in the right direction will add up to an outcome representing 10x growth on a transformative scale.
2. Apply continuous integration at every step of the process — while integrating demand with sourcing, and sourcing with screening, — to build a visible pipeline of value creation.
3. Leverage change management tools and basic automation structures (like machine learning), to control the overall change effort. This will minimize the impact on workers and avoid distractions, leading to maximum organizational benefit.
How can continuous improvement make a step-up change in organizational transformation?
“Kaizen is about changing the way things are. If you assume that things are all right the way they are, you can’t do kaizen. So change something!”
— Taiichi Ohno, father of the Toyota production system
Fundamentally, continuous improvement doesn’t change the dynamics of a team or a company. Neither should stakeholders and users change their behavior. Also, it isn’t about setting a high pace. It simply drives every employee to deliver a 100% to one project, one adaptation or one idea, at a time.
To get there, try to generate or apply new technologies in continuous organizational processes. I’ve listed a mix of popular methodologies and technological approaches below, in no particular order:
1. Agility: As you re-imagine the future of work within your organization, ensure that agility stays at pace, with the rapidity of continuous innovation.
2. Digital methodologies: Your organization’s continuous improvement tool can benefit immensely from digitization.
3. Design thinking: Your firm is busy curating exceptional client experiences in real time. That makes design principles all the more critical, as you envision the cognitive capabilities to co-create best business solutions.
4. DevOps: DevOps is crucial to build a strong transformation strategy. With it, you can identify patterns and uncover new revenue streams.
That being said, the biggest enemy of continuous improvement is complacency (or the idea of a “comfort zone”). And there’s just one way to avoid it. You can be self-reflective and objective, while evaluating yourself or your team. At the end of the day, an honest self-reflection leads to better focus. And a better focused workforce always delivers toward a single business vision.
Responses