Understanding SAP’s Organizational Structure: A Guide to Streamlining Business Operations
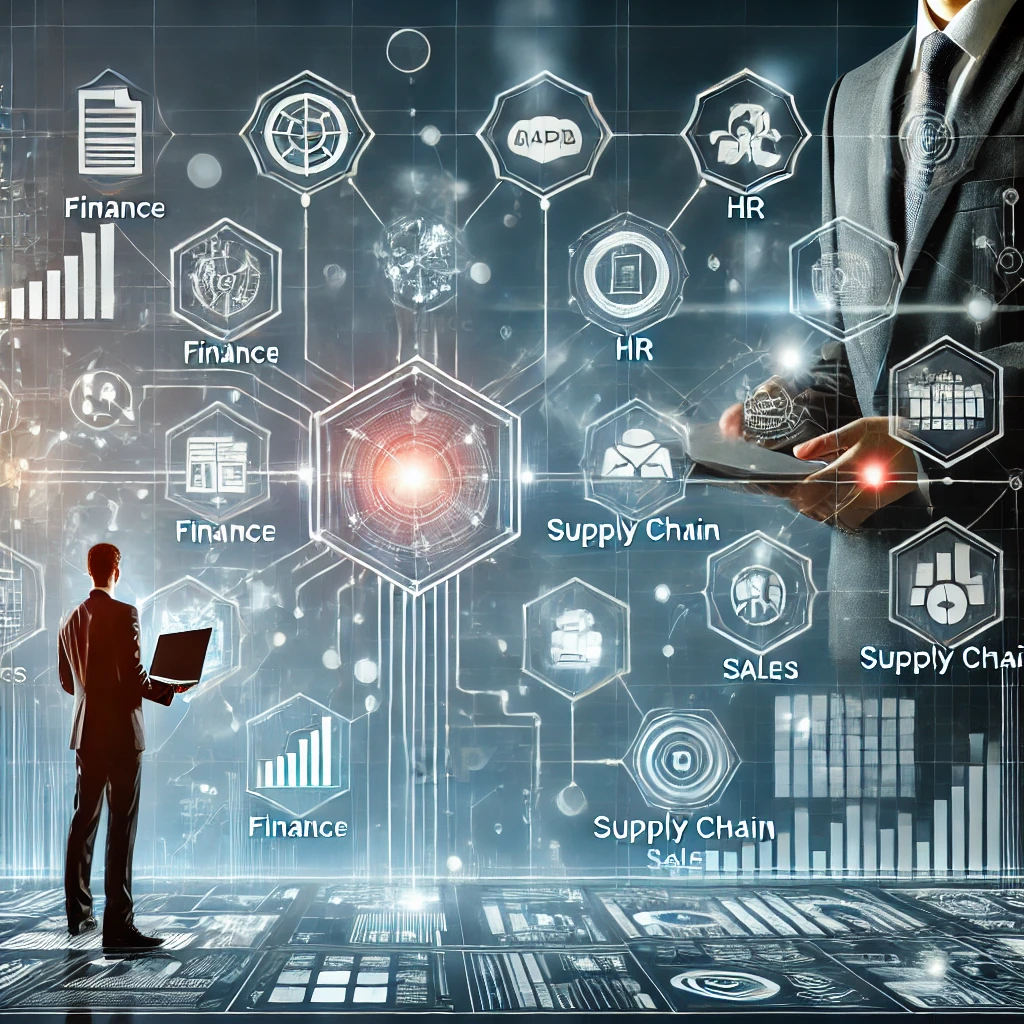
In today’s fast-paced corporate world, efficient management of resources, processes, and data is essential. SAP Materials Management (SAP MM) offers a robust organizational framework designed to meet these needs. Its hierarchical structure integrates various organizational units, ensuring seamless collaboration between business and legal entities. Let’s dive into the details to understand how SAP MM is structured and how it supports organizational efficiency.
Why is This Structure Important?
SAP’s organizational hierarchy streamlines operations, improves data accuracy, and ensures compliance with financial and legal standards. Businesses can use this framework to:
- Optimize resource management.
- Enhance inventory tracking.
- Improve procurement processes.
The Six Levels of SAP MM Organizational Structure
SAP MM’s framework consists of six interconnected levels, each with a specific purpose. These include:
1️⃣ Client
2️⃣ Company Code
3️⃣ Plant
4️⃣ Storage Location
5️⃣ Purchasing Organization
6️⃣ Purchasing Group
Each level plays a vital role in streamlining operations and aligning processes with business goals.
1️⃣ Client: The Foundation
- The Client is the most fundamental unit in the SAP hierarchy.
- From a business perspective, the client represents a corporate group.
- It represents a commercial organizational unit and maintains a unique set of master data with independent table sets.
- Data at the Client level is universal and valid across all organizational levels.
- Example: A company’s SAP system may have different clients for development, quality assurance, and production.
2️⃣ Company Code: The Legal Entity
- The Company Code represents a distinct legal entity within the organization.
- It maintains its own balance sheet and profit & loss statement and requires a General Ledger.
- In a conglomerate, multiple company codes can coexist within the same SAP instance, each representing a separate entity.
- Example: A multinational corporation with subsidiaries in different countries might use separate company codes for each subsidiary to ensure legal and financial compliance.
3️⃣ Plant: The Operational Hub
- A Plant is the location where purchasing, production, inventory, and sales activities are conducted.
- Plants can operate as independent facilities with unique processes and materials.
- Key elements of a plant include: Address, Tax jurisdiction code, Factory calendar, & Material master data.
- Example: A manufacturing company may define different plants for its factories, each handling specific production lines or products.
4️⃣ Storage Location: Managing Inventory
- Storage Locations within a plant represent physical areas where stock is stored.
- These locations help track material quantities and update the General Ledger for inventory changes.
- Use Cases: Material received from a vendor. Material used in production. Material sold to a customer.
5️⃣ Purchasing Organization: Procurement Management
- The Purchasing Organization manages procurement activities for one or multiple plants.
- It negotiates with vendors, sets pricing terms, and ensures smooth supply chain operations.
6️⃣ Purchasing Group: Focused Procurement
- The Purchasing Group focuses on specific procurement tasks, like vendor coordination or material sourcing.
Key Takeaways
Understanding SAP MM organizational structure is critical for anyone involved in supply chain, operations, or finance. It enables businesses to create a robust system for efficient operations and informed decision-making.
Responses